Technology
Our technology will change the aviation industry
Combining Technology and Industrial Strength
Our production process is based on Power-to-Liquid technology and focuses on the Fischer-Tropsch pathway. The underlying process chain covers the entire carbon cycle from CO2 capture to fuel combustion. Together with our partners, we combine technology versatility and development potential to achieve the highest conversion efficiencies.
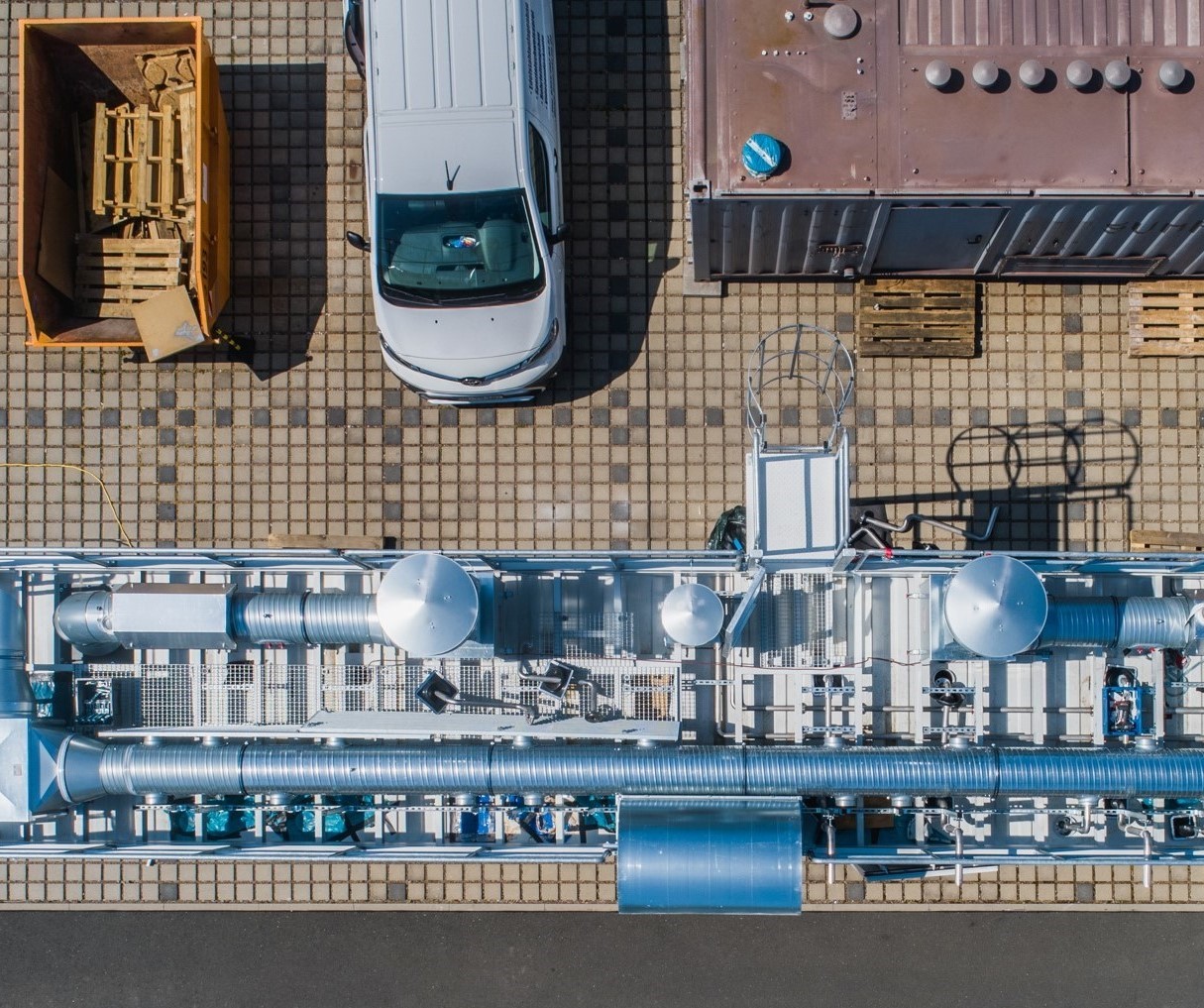
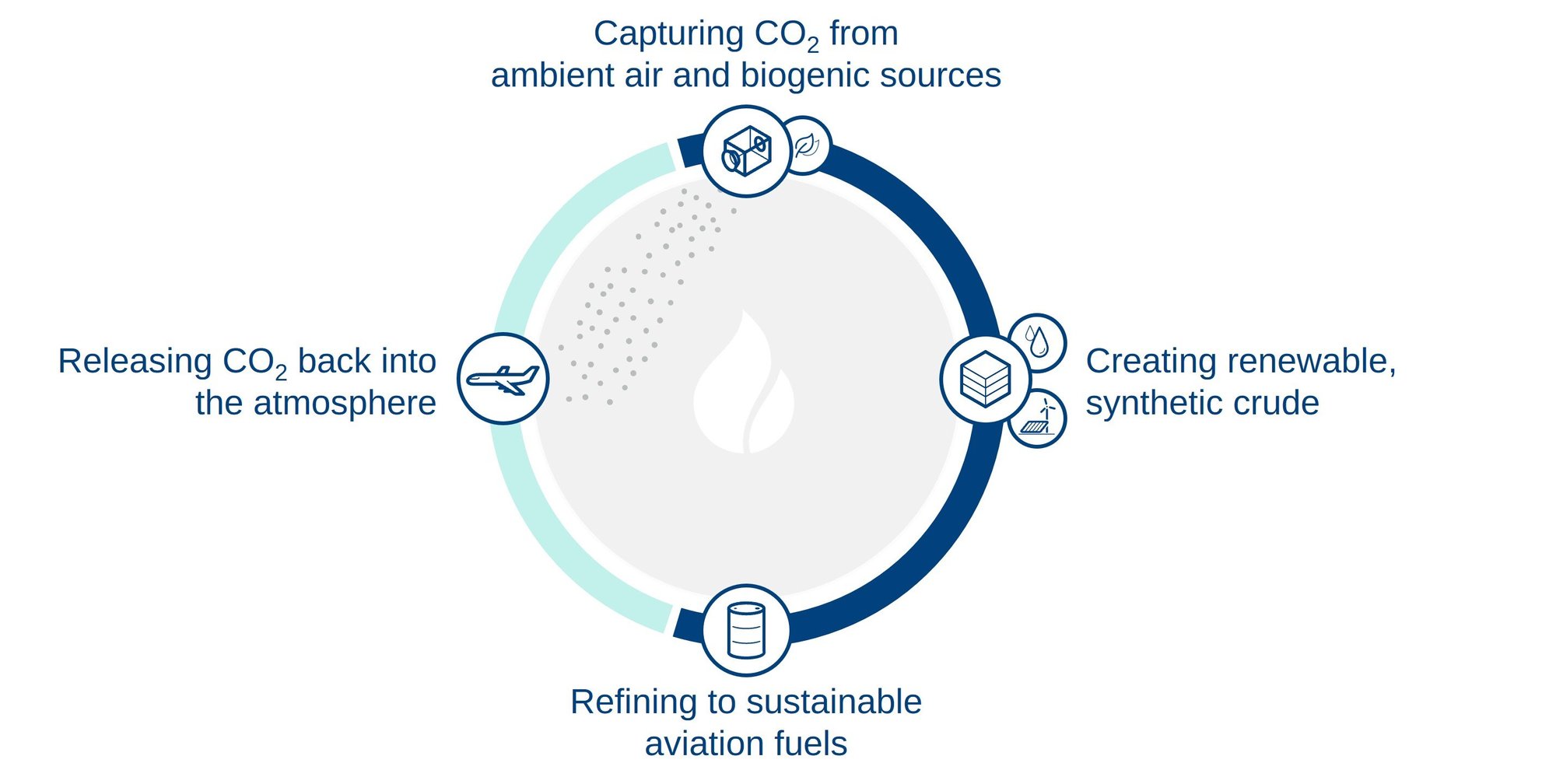
The carbon cycle shows, how we can produce unlimited renewable fuels without releasing more CO2 from fossil sources into the atmosphere.
-
Recycling carbon dioxide from air and biogenic sources
In the first step, CO2 is extracted from the air using innovative Direct Air Capture (DAC) systems. Together with recycled CO2 from biogenic waste gas streams, which will initially supplement the CO2 supply, it is one of the main feedstocks for the second process step.
-
Creating renewable, synthetic crude
In the second process step, syngas is produced from CO2 and water by using renewable electricity. This can be achieved either via high-temperature co-electrolysis or by a technology combination of low-temperature electrolysis for hydrogen production coupled with a Reverse-Water-Gas-Shift reactor.
The syngas, a mixture of hydrogen and carbon monoxide is then converted to hydrocarbons of different chain lengths in a Fischer-Tropsch reactor under the influence of pressure, temperature, and catalysts. A synthetic, renewable crude oil equivalent is produced. Waste heat from the synthesis is captured as steam and can be used as input to the co-electrolyzer to increase process efficiency or for district heating.
-
Refining to Sustainable Aviation Fuel
In the third process step, the renewable synthetic crude can be refined into the products of choice, such as kerosene, diesel, gasoline, waxes and other chemicals. However, chemistry imposes some limitations on the fractions that can be obtained. At Norsk e-Fuel, we are optimizing our processes and products for the aviation industry, where we believe they are most needed. As a result, we are able to convert 70-80% of our products into e-Kerosene, which can be used in existing infrastructures and meets ASTM standards.
-
Using the e-Fuel and releasing the carbon dioxide into the atmosphere
In the fourth step, the sustainable aviation fuel is transported to the airport. In the aircraft's combustion engine, the carbon contained in the fuel is released back into the atmosphere. At this point, we close the cycle when the CO2 is captured again by DAC or absorbed by plants. Including steps 1-4, the process is fully circular and enables unlimited renewable transportation without releasing more CO2 from fossil sources into the atmosphere.
Our unique technology approach
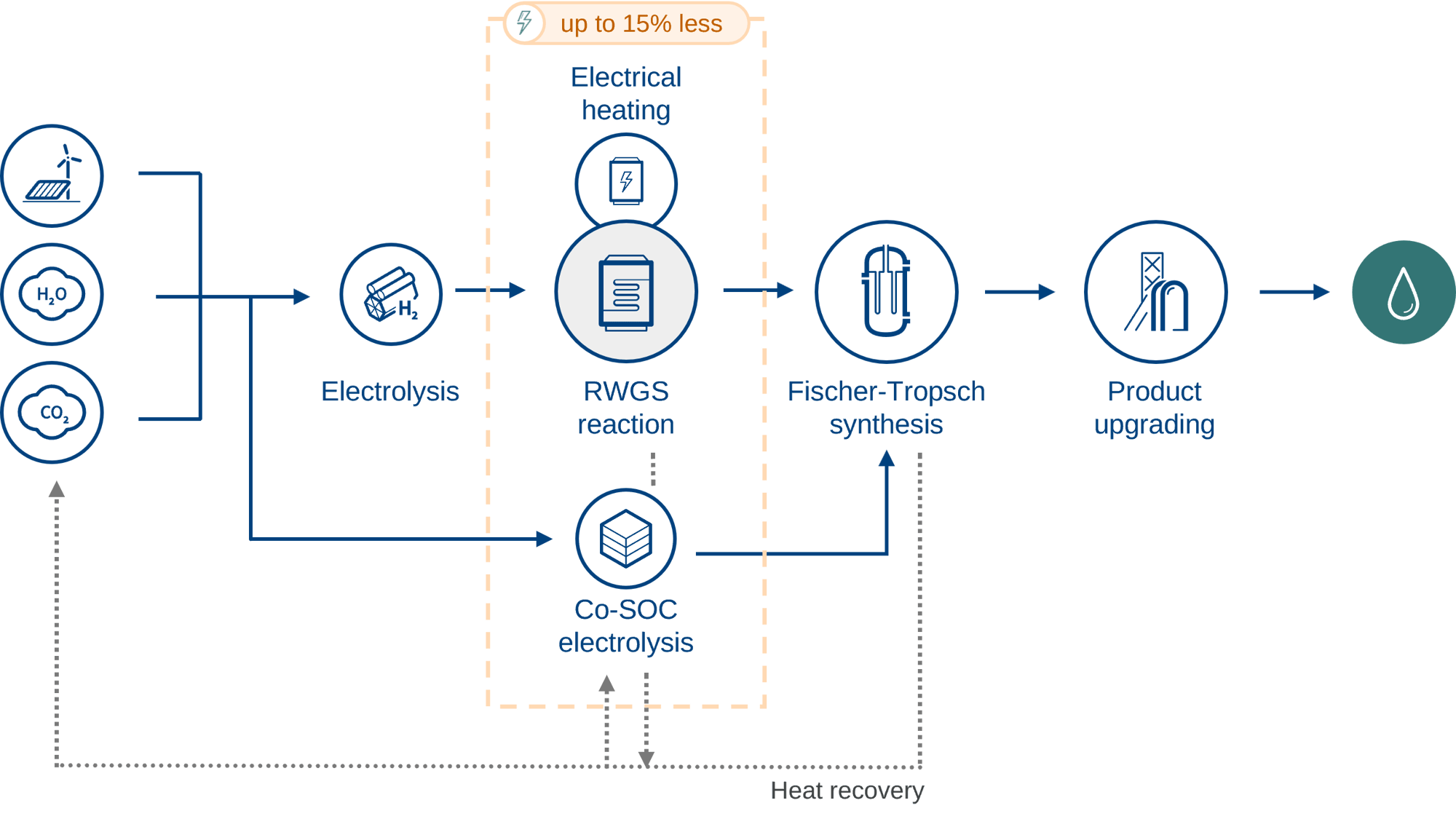
As described above, there are two technological approaches to syngas production. Norsk e-Fuel will leverage the individual advantages of both technologies by validating the approaches within the first plant. This will allow us to take advantage of the synergies and at the same time prove the most promising and efficient ways of e-Fuel production in parallel.
-
Innovative state-of-the-art approach
The production pathway via the low-temperature electrolyzer for hydrogen production and the Revers-Water-Gas-Shift Reactor for syngas production is based on well-known and proven technology units, which will reduce the technological risk that is inherent in all first-of-a-kind industrial projects. And while the technologies are scaled, ready-to-use and reliable, they offer great potential for technological improvement. In addition, they are commercially available on the market today in larger volumes, allowing us to quickly scale up.
-
Cutting-edge approach
The process based on a high-temperature co-electrolyzer to produce syngas in a single step, allows us to generate e-Fuels with higher efficiencies. This is important to reduce the amount of electricity needed and the associated environmental impact, but also for the economic impact. Less electricity means lower production costs, which in turn means lower prices for e-Fuels.
Our technology partners
It is our goal to always use the most efficient technologies available on the market. The licenses for the technology set-up will be provided by our strong network of partners. The affiliation to our shareholders brings the important advantage of direct access to core technologies. Renown partners in the field will complete the technological composition of our plant design.
e-RWGS, Fischer-Tropsch and upgrading unit by Axens and Paul Wurth (SMS group)
The novel process set-up for the main production stream combines a Reverse-Water-Gas-Shift (RWGS) unit co-developed by Axens and Paul Wurth, a Fischer-Tropsch unit and an upgrading unit (Gasel®). Both RWGS and Gasel® are under exclusive license of Axens. The combination of the singular technology units of Axens and their optimization for maximized e-Kerosene production are in themselves an innovation. To further push the boundaries, Paul Wurth has designed a unique electrical heating system for the RWGS, avoiding unnecessary burning of fossil fuel or hydrogen. The deep integration of the process scheme allows to optimize the energy efficiency as well as the carbon conversion of the plant.
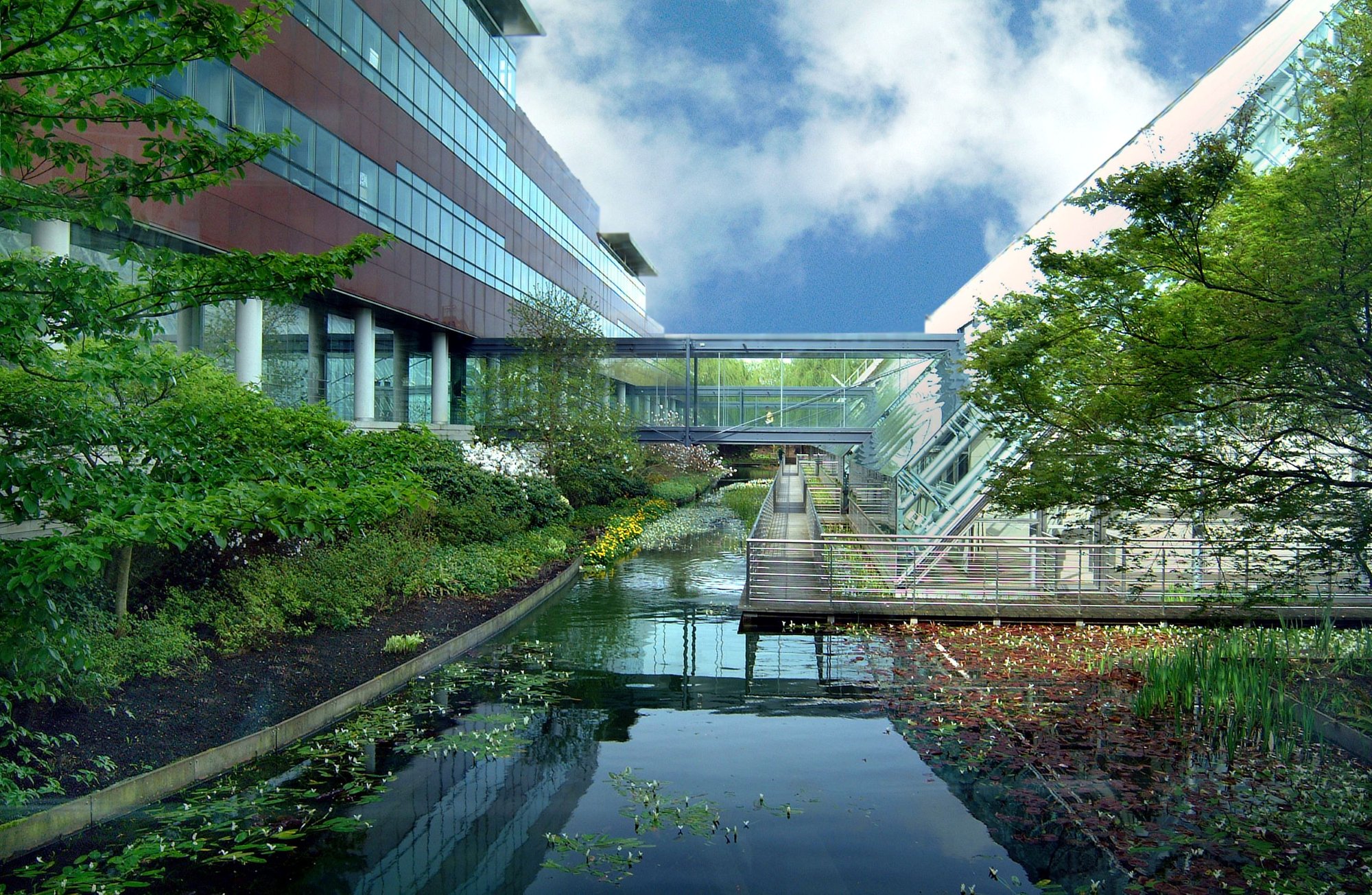
Electrolyzer technology by Sunfire
Sunfire-SynLink SOEC ® (Solid Oxide Electrolyzer Cell) is the world-leading high-temperature electrolysis solution based on solid oxide cells. The electrolyzer uses steam and CO2 as feedstock to produce renewable syngas in only one process step. Smart integration of waste heat and CO2 sources reduces electricity demand. The integrated process reuses for example process heat from the Fischer-Tropsch reactor to create the needed steam for the electrolysis process. This increases the output of the plant, resulting in 30 % more product from the same electricity input in comparison to the production via a gas-fired RWGS pathway.
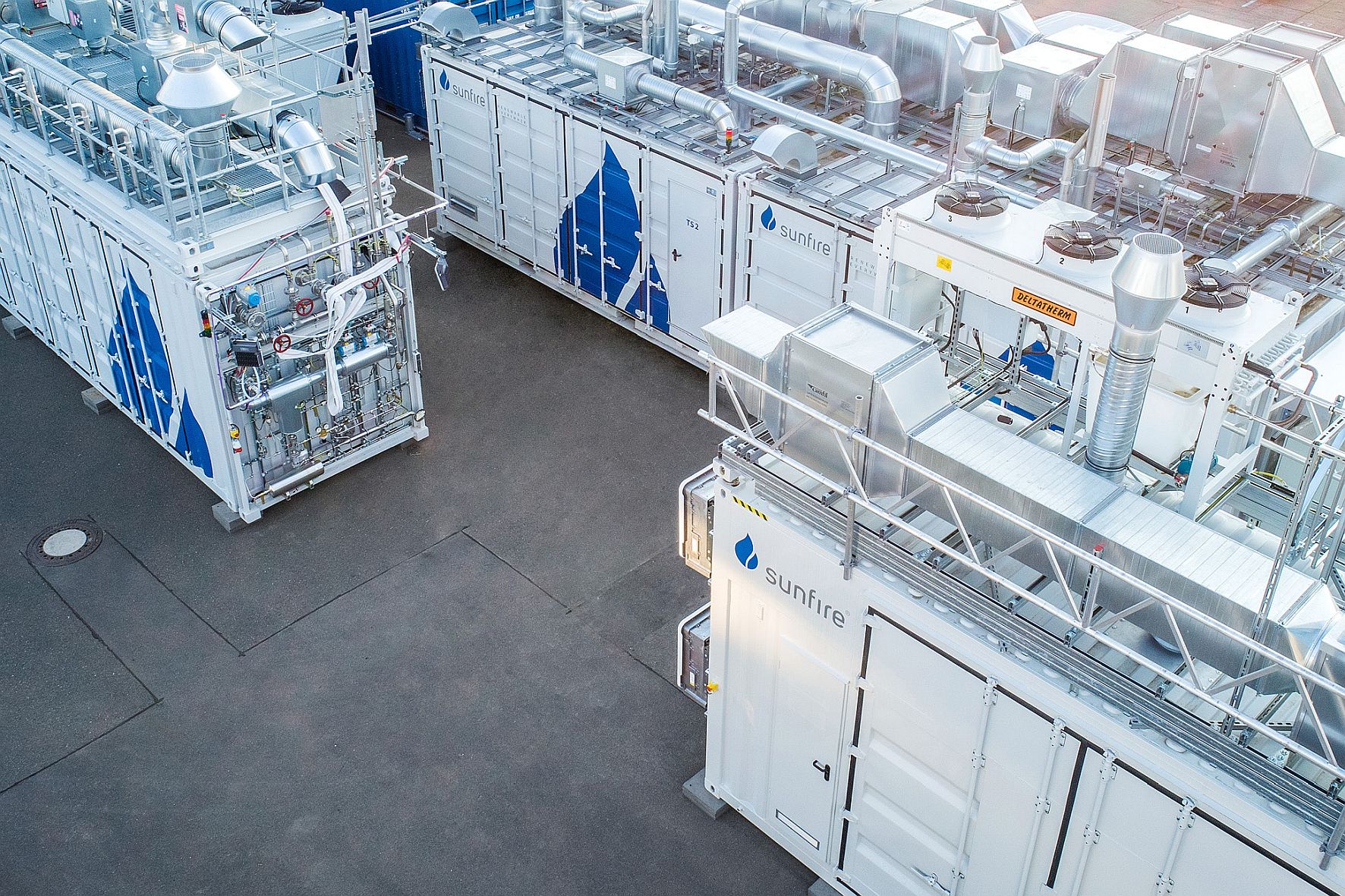
Direct air capture technology by Climeworks
The Climeworks direct air capture technology captures carbon dioxide directly from the air. The machines consist of modular CO₂ collectors that can be stacked to build machines of any size. They are powered solely by renewable energy or energy-from-waste. The CO2 collectors selectively capture carbon dioxide in a two-step process. First, air is drawn into the collector with a fan. Carbon dioxide is captured on the surface of a highly selective filter material that sits inside the collectors (“adsorption”). Second, after the filter material is full with carbon dioxide, the collector is closed. The temperature is increased to between 80 and 100 °C - this releases the carbon dioxide (“desorption”) and it can be collected in higher purity and concentration. The air-captured carbon dioxide can either be upcycled into climate-friendly products such as carbon-neutral fuels and materials, or completely removed from the air by safely storing it.
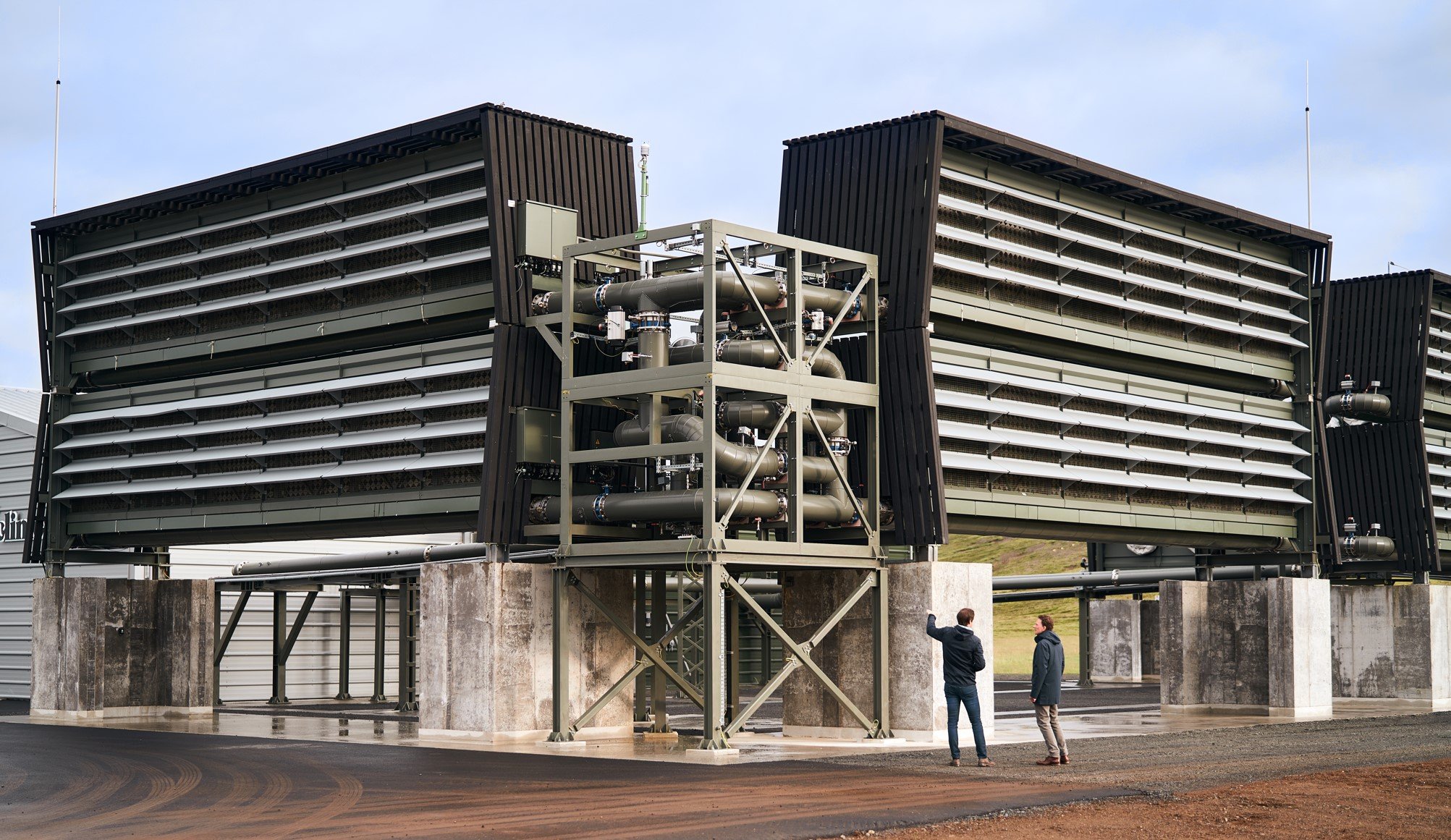